J. R. Senft: Free Piston Stirling Engines, Kartoniert / Broschiert
Free Piston Stirling Engines
(soweit verfügbar beim Lieferanten)
- Verlag:
- Springer Berlin Heidelberg, 06/1985
- Einband:
- Kartoniert / Broschiert, Paperback
- Sprache:
- Englisch
- ISBN-13:
- 9783540154952
- Artikelnummer:
- 2957931
- Umfang:
- 284 Seiten
- Sonstiges:
- 41 SW-Abb.,
- Ausgabe:
- Softcover reprint of the original 1st edition 1985
- Copyright-Jahr:
- 1985
- Gewicht:
- 492 g
- Maße:
- 247 x 170 mm
- Stärke:
- 23 mm
- Erscheinungstermin:
- 1.6.1985
- Hinweis
-
Achtung: Artikel ist nicht in deutscher Sprache!
Inhaltsangabe
List of Contents.- 1 Introduction.- Definition and Nomenclature.- History.- Thermodynamics of the Stirling Cycle.- The Stirling Cycle Refrigerator.- The Stirling Cycle Heat Pump.- The Stirling Cycle Pressure Generator.- Practical Stirling Engines.- Mechanical Arrangements.- Piston-Displacer in the Same Cylinder.- Pistons.- Displacers.- Advantages of the Piston and Displacer System.- Piston and Displacer in Separate Cylinders.- Single-Acting Engines.- Double-Acting Engines.- Reciprocator Drives: Kinematic or Free-Piston.- Kinematic Drive Engines.- Free-Piston Engines.- Advantages of Free-Piston Stirling Engines..- Disadvantages of Free-Piston Stirling Engines.- Closure.- References.- 2 Free-Piston Stirling Engines.- I: Elementary Aspects.- How a Free-Piston Stirling Engine Works.- Beale Free-Piston Stirling Demonstrator Engine.- Types and Classifications of Free-Piston Stirling Engines.- Single-Acting Free-Piston Stirling Engines.- i) Two-Piston Arrangements.- ii) Piston-Displacer Arrangements.- iii) Split-Stirling Systems.- Double-Acting Free-Piston Stirling Engines.- Hybrid Stirling Engines.- Pendulum Free-Piston Stirling Engines.- Diaphragm Free-Piston Stirling Engines.- Duplex Free-Piston Stirling Engines.- II; Dynamics of Free-Piston Stirling Engines.- Vibrating Systems; An Elementary Review.- Degrees of Freedom.- Free Vibration.- Simple Harmonic Motion.- Viscous Damping.- Equation of Motion.- Non-Viscous Damping.- Systems with More Than One Degree of Freedom.- Non-Linear Systems.- Vector Representation of Vibrating Systems.- Vector Addition and Subtraction.- Force Representation.- Vector Force Polygon.- Work Input and Power Consumption.- Free-Piston Stirling Engines as Vibrating Systems.- Vector Representation of Free-Piston Stirling Engines.- a) Piston-Displacer System, Both Elements Sprung to Ground.- b) Piston-Displacer System with the Displacer Sprung to Ground.- c) Piston-Displacer System with the Displacer Sprung to the Piston.- d)Split-Stirling Engine.- e)Two-Piston Stirling Engine.- f)Free-Cylinder Stirling Engine.- g)Double-Acting Stirling Engine.- III; Some Practical Considerations.- Piston Centering.- Seals.- Bearings.- Hydrodynamic Bearings.- Hydrostatic Bearings.- Materials.- Springs.- Spring Stiffness.- Closure.- References.- 3 Theoretical Analysis and Design.- Elementary Design Tools.- Ideal Cycle.- Beale Number.- Frequency Estimation.- Efficiency.- First Order Analysis Methods.- Schmidt Analysis.- Free-Piston Engine Dynamics.- Linearization of Pressure.- Second Order Analysis.- Basic Power Calculation.- Loss Mechanisms.- Available Programs.- Third Order Analysis.- Analytic Design of Free-Piston Engines.- Nomenclature.- References.- 4 The Sunpower Engines.- Chronology.- Sunpower Advice to the Designer of Free-Piston Stirling Engines.- Free-Piston Engines and Rotary Motion.- Guidelines for Free-Piston Stirling Engine Application.- References.- 5 Hybrid or Ringbom-Stirling Engines.- The Hybrid Concept.- The Ringbom Engine.- Overdriven Mode Operation.- Comparison with Free-Piston Engines.- Basic Approaches to Design of Hybrids.- The Overdriven Mode Operation Concept.- Stable Operation.- First Order Analysis.- Isothermal Model for Hybrid Ringbom-Stirling Engines.- A Criterion for Overdriven Mode Operation.- Overdriven Mode Theorem.- Application of the Theorem.- Some Practical Considerations.- Displacer Drive Loss.- Top End Tuning.- General Design Guidelines.- Practical Ringbom-Stirling Engines.- Nomenclature.- References.- 6 Diaphragm Stirling Engines: The Harwell Thermo-Mechanical Generator.- Diaphragms.- Displacer Design.- The Alternator.- System Dynamics.- Losses.- Viscous Losses.- Regenerator Losses.- Imperfect Heat Conduction.- Computed Losses.- Increasing the Generator Power.- Operating Experience.- Conclusions.- Nomenclature.- References.- 7 Small Free-Piston Stirling Engine: Power Systems fofr the Artificial Heart.- The Artificial Heart.- Stirling Engines in Artificial Hearts.- The Aerojet General Engi
Klappentext
DEFINITION AND NOMENCLATURE A Stirling engine is a mechanical device which operates on a closed regenerative thermodynamic cycle with cyclic compression and expansion of the working fluid at different temperature levels. The flow of working fluid is controlled only by the internal volume changes, there are no valves and, overall, there is a net conversion of heat to work or vice-versa. This generalized definition embraces a large family of machines with different functions; characteristics and configurations. It includes both rotary and reciprocating systems utilizing mechanisms of varying complexity. It covers machines capable of operating as a prime mover or power system converting heat supplied at high tempera ture to output work and waste heat at a lower temperature. It also covers work-consuming machines used as refrigerating systems and heat pumps abstracting heat from a low temperature source and delivering this plus the heat equivalent of the work consumed to a higher tem perature. Finally it covers work-consuming devices used as pressure generators compressing a fluid from a low pressure to a higher pres sure. Very similar machines exist which operate on an open regen erative cycle where the flow of working fluid is controlled by valves. For convenience these may be called Ericsson engines but unfortunate ly the distinction is not widely established and regenerative machines of both types are frequently called 'Stirling engines'.
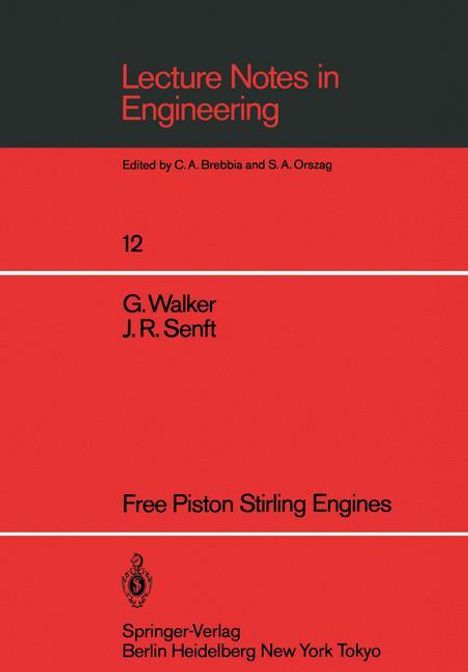